The Scientific Research Behind Porosity: A Comprehensive Overview for Welders and Fabricators
Understanding the intricate devices behind porosity in welding is critical for welders and makers aiming for remarkable workmanship. From the make-up of the base materials to the intricacies of the welding procedure itself, a wide variety of variables conspire to either intensify or reduce the visibility of porosity.
Comprehending Porosity in Welding
FIRST SENTENCE:
Examination of porosity in welding exposes crucial understandings into the stability and quality of the weld joint. Porosity, defined by the visibility of tooth cavities or gaps within the weld metal, is a typical problem in welding procedures. These gaps, otherwise properly attended to, can endanger the architectural honesty and mechanical residential or commercial properties of the weld, bring about possible failures in the completed product.

To discover and evaluate porosity, non-destructive screening techniques such as ultrasonic testing or X-ray assessment are commonly used. These strategies allow for the identification of interior issues without compromising the integrity of the weld. By evaluating the size, shape, and distribution of porosity within a weld, welders can make informed decisions to improve their welding processes and achieve sounder weld joints.

Aspects Affecting Porosity Development
The incident of porosity in welding is influenced by a myriad of variables, ranging from gas securing effectiveness to the complexities of welding parameter setups. Welding parameters, including voltage, existing, travel rate, and electrode type, likewise influence porosity formation. The welding strategy employed, such as gas steel arc welding (GMAW) or secured metal arc welding (SMAW), can affect porosity development due to variations in warmth distribution and gas protection - What is Porosity.
Results of Porosity on Weld Quality
The existence of porosity additionally damages the weld's resistance to deterioration, as the entraped air or gases within the spaces can react with the surrounding atmosphere, leading to degradation over time. Additionally, porosity can prevent the weld's capacity to stand up to pressure or impact, more endangering the general quality and integrity of the bonded structure. In crucial applications such as aerospace, automotive, or architectural buildings, where safety and durability are extremely important, the damaging impacts of porosity go now on weld quality can have extreme repercussions, stressing the value of minimizing porosity via appropriate welding techniques and treatments.
Methods to Decrease Porosity
In addition, using the suitable welding specifications, such as the proper voltage, current, and travel speed, is vital in protecting against porosity. Maintaining a constant arc length and angle throughout welding additionally aids lower the likelihood of porosity.

Additionally, choosing the best shielding gas and preserving click here to read appropriate gas circulation rates are vital in decreasing porosity. Making use of the suitable welding strategy, such as back-stepping or employing a weaving movement, can also aid distribute warmth uniformly and minimize the chances of porosity formation. Making sure appropriate ventilation in the welding atmosphere to remove any potential sources of contamination is vital for achieving porosity-free welds. By applying these strategies, welders can successfully reduce porosity and produce top quality welded joints.
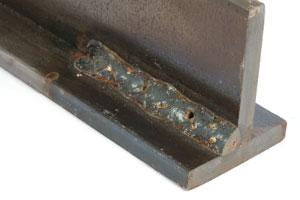
Advanced Solutions for Porosity Control
Carrying out advanced modern technologies and ingenious approaches plays a pivotal function in attaining exceptional control over porosity in welding look at here now procedures. Additionally, utilizing innovative welding techniques such as pulsed MIG welding or customized atmosphere welding can likewise assist minimize porosity issues.
An additional advanced service includes making use of advanced welding devices. Using equipment with integrated features like waveform control and advanced power sources can boost weld quality and minimize porosity risks. The execution of automated welding systems with specific control over criteria can significantly minimize porosity defects.
Furthermore, incorporating advanced surveillance and inspection technologies such as real-time X-ray imaging or automated ultrasonic screening can assist in detecting porosity early in the welding procedure, permitting prompt rehabilitative activities. In general, integrating these advanced solutions can greatly boost porosity control and improve the general quality of welded parts.
Final Thought
In verdict, comprehending the science behind porosity in welding is essential for welders and producers to produce top notch welds - What is Porosity. Advanced services for porosity control can better enhance the welding procedure and guarantee a solid and dependable weld.